Sustainability
Environment
MITHELA TEXTILE INDUSTRIES LIMITED, a pioneering venture of the MITHELA GROUP, exemplifies the group's commitment to quality, innovation, and sustainability in the textile industry. Since its inception in 2002, MITHELA TEXTILE has set a global benchmark by becoming the world’s first LEED Platinum-certified woven textile factory.
ETP
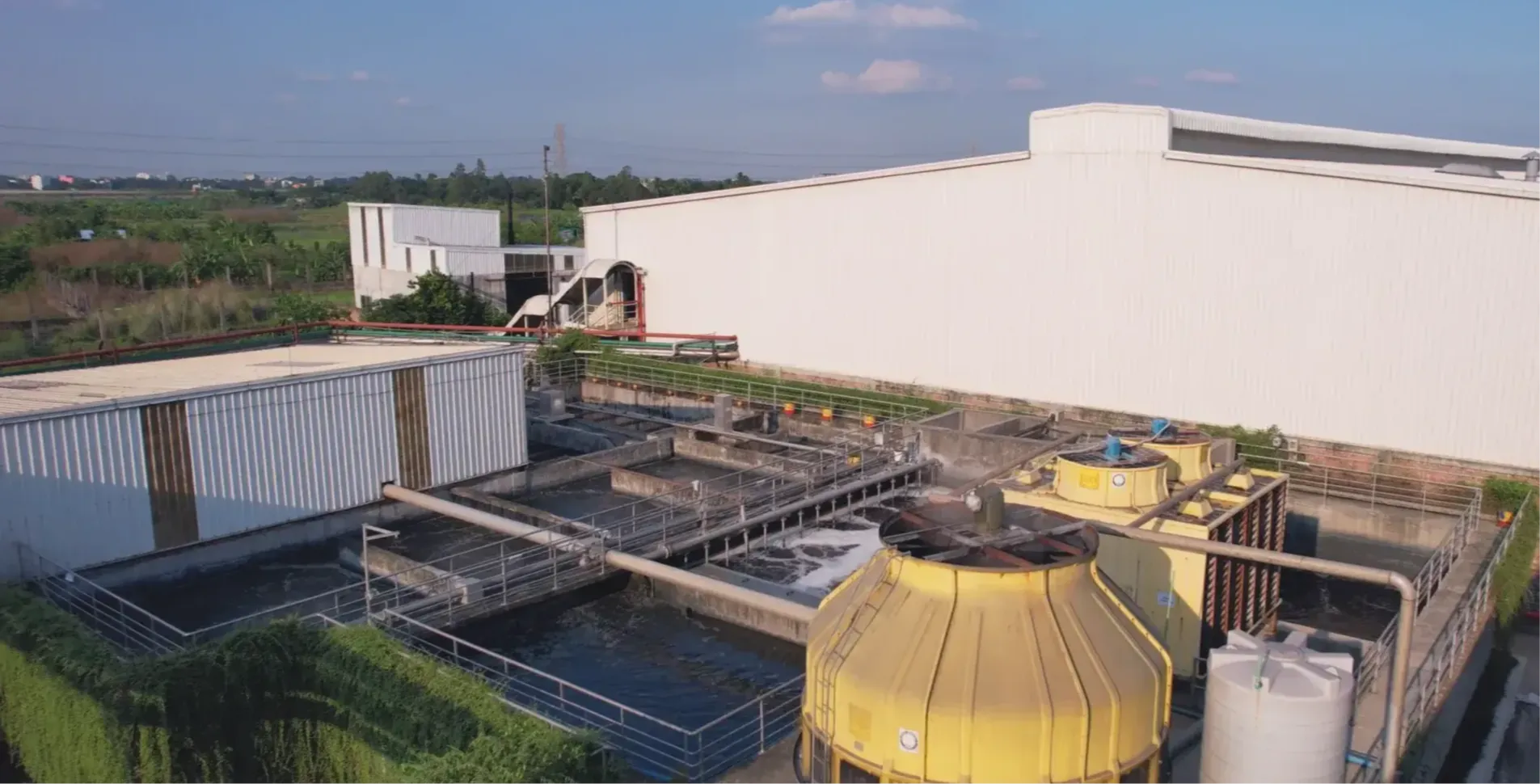
We process the water we utilize and re-use it
With the help of our latest Japanese technology, the PVA gel-based biological ETP, we process the toxic water that remains after dyeing woven materials.
This technology helps in processing 50% of water for re-use. And we use this 50% of water for irrigation.
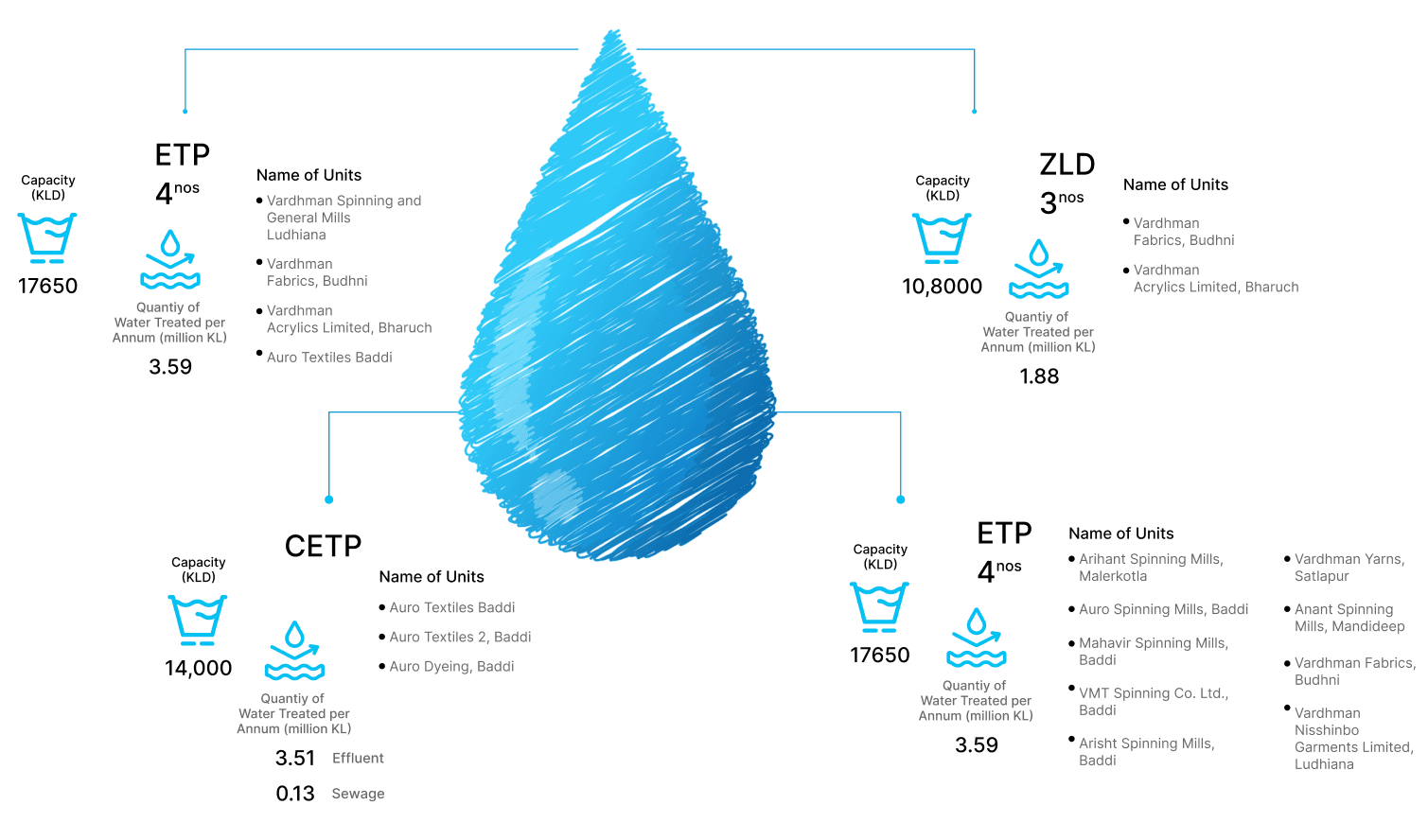
We have taken great strides in conserving and recharging water sources around all our plants and facilities. We have 9 Sewage Treatment Plants and 4 Effluent Treatment Plants across our units, out of which 3 are Zero Liquid Discharge facilities.
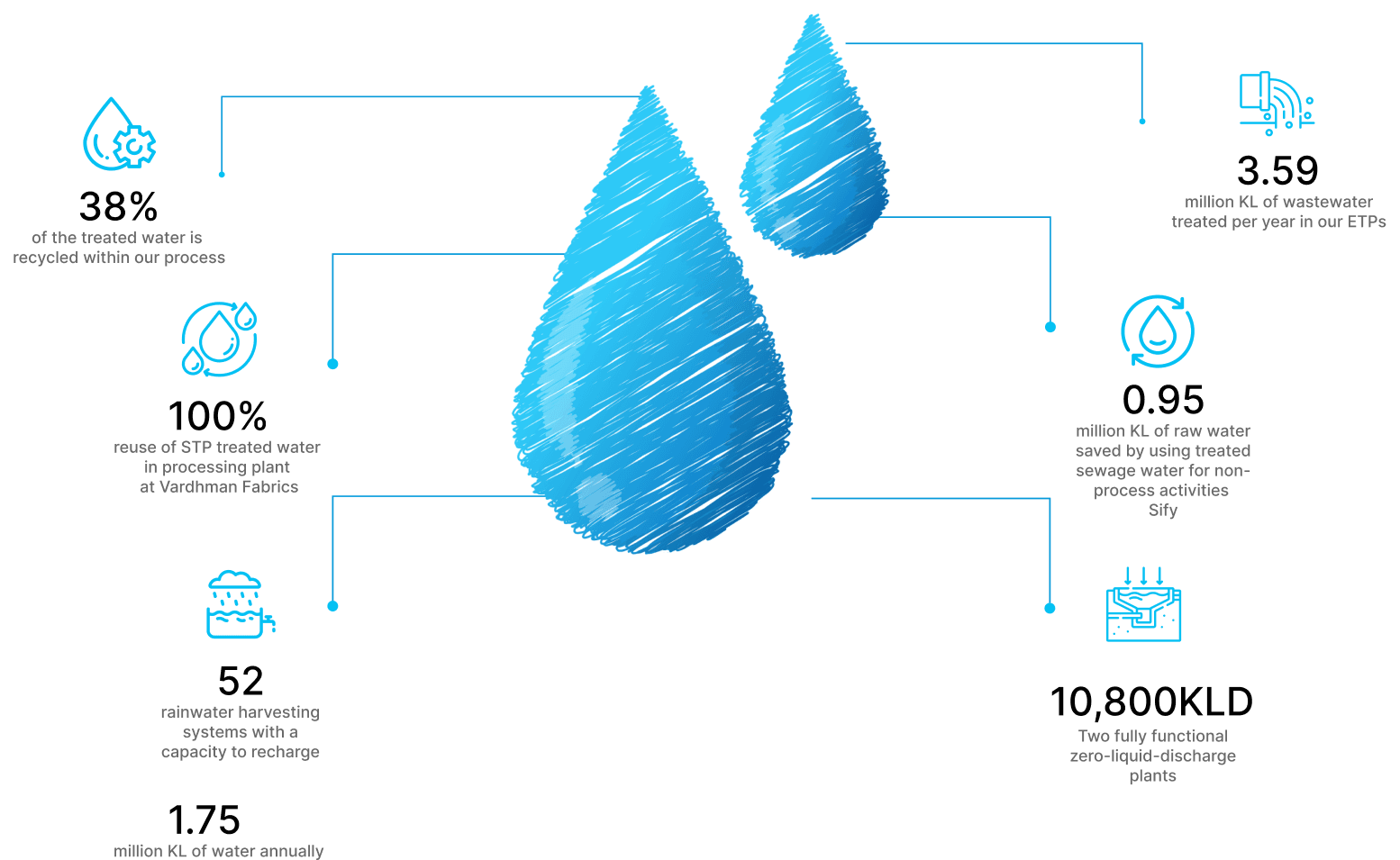
CRP/Caustic Recovery Plant
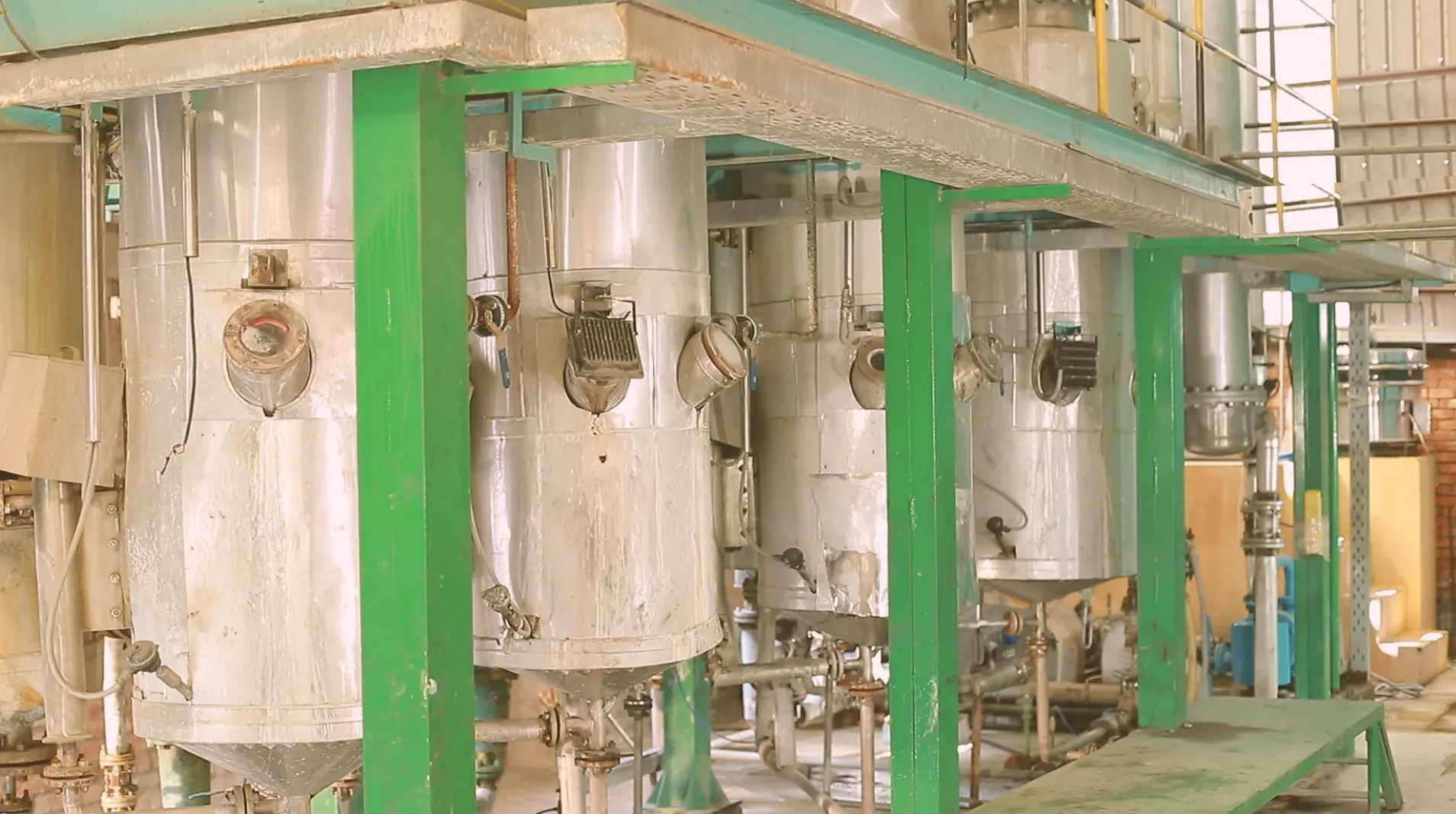
We own and operate a Caustic Recovery Plant (CRP)
To reduce caustic soda from our products we generally do a ‘Caustic Recovery’ process that dilutes the caustic soda solution from the textile, which eventually comes out from the mercerizing machines. Our CRP does at least 90% Caustic recovery
Energy Save/Husk/Husk burn
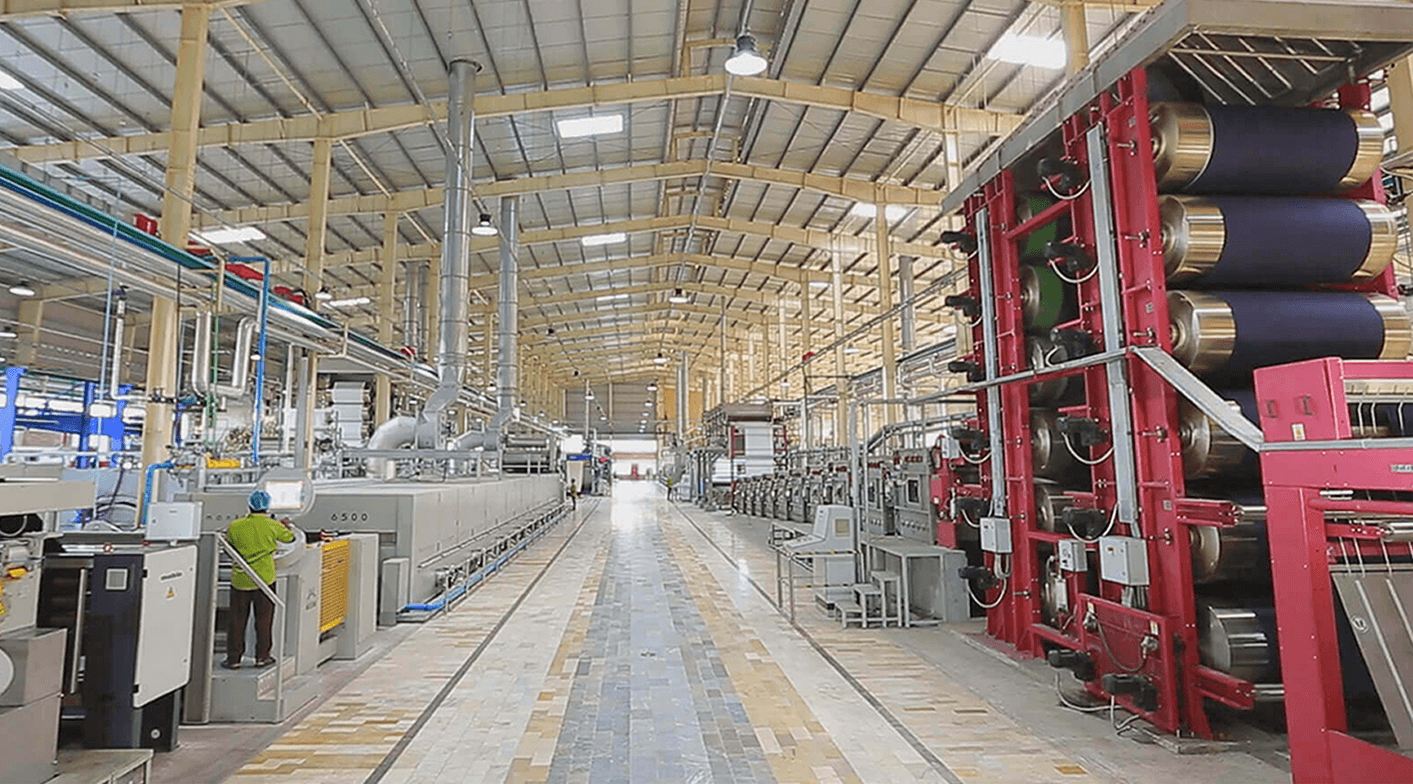
We also save energy
MTIL has its own energy plant that produces heat to burn the rice husk. This heat is then further transformed to steam energy, to run the fuel-saving economizer generator. So basically, we save almost 68% of energy from the total requirement of any textile factory that is into dyeing and manufacturing clothes such as woven fabric chinos, non-denim wear, etc.
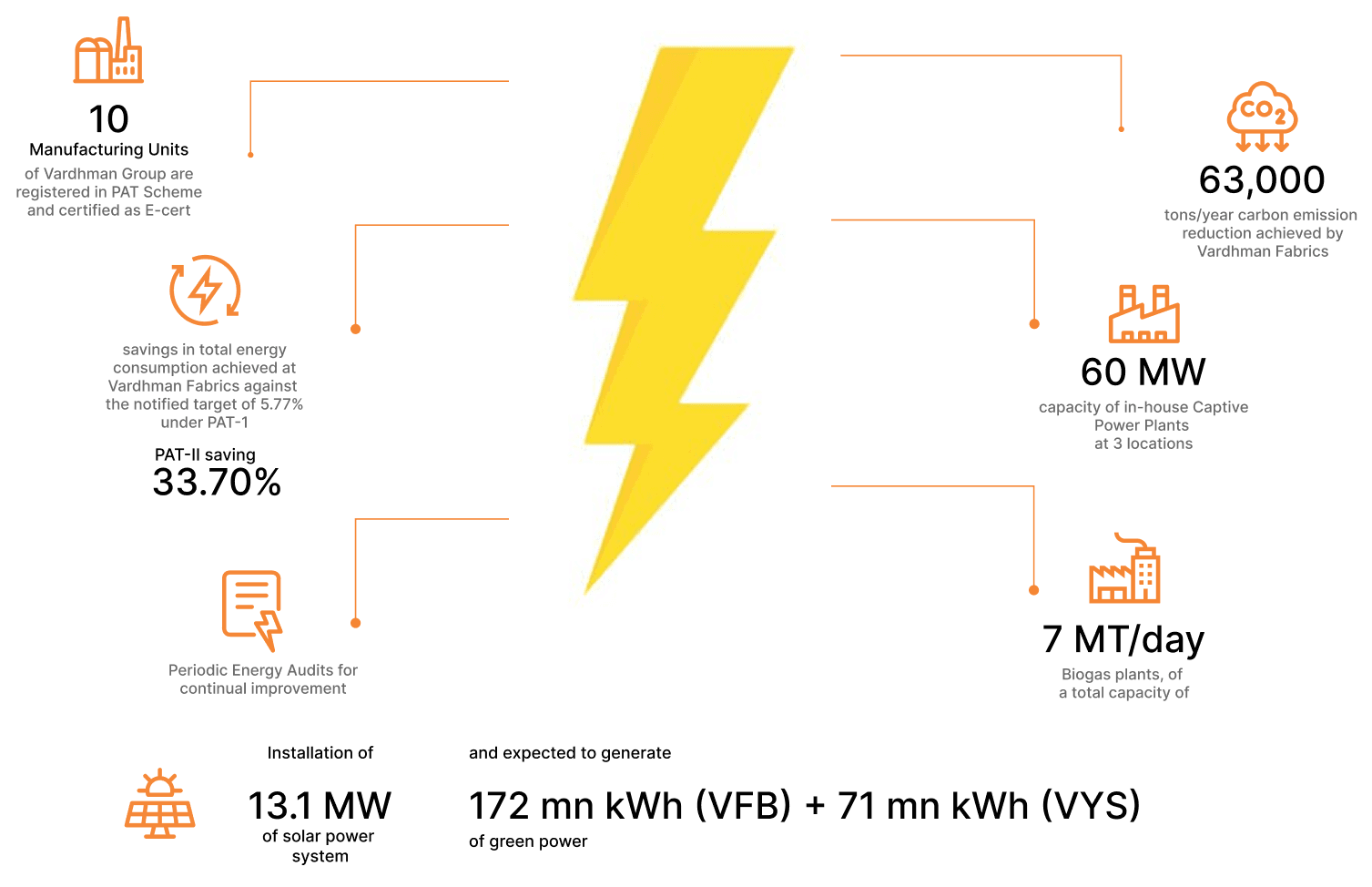